Maximizing Reliability and Ease of Management in a Solar Power Plant
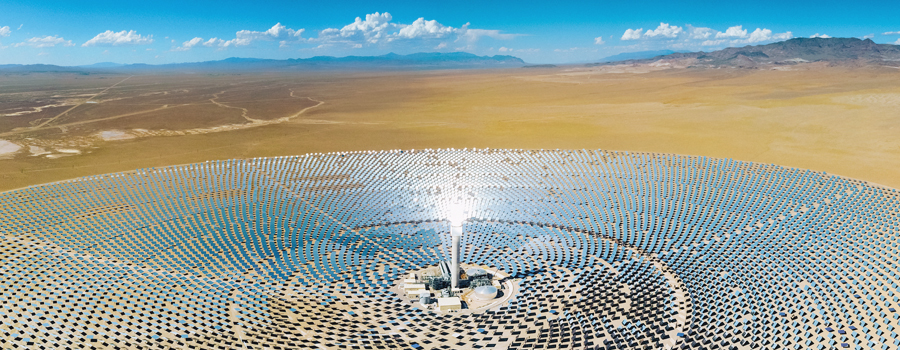
Background
The transition from fossil fuels to renewable energy sources is accelerating in countries around the world. On a global scale, there are more power plants going online that use clean sources, than coal and natural gas combined. One of the most popular forms of renewal energy is solar, especially in regions that lack strong winds and large rivers.
In the northern part of Chile lies the Atacama Desert. Its nearly moisture-free climate, combined with an abundance of year-round sunlight, makes it an ideal location to construct a solar power plant. The new 110-megawatt plant, named Cerro Dominador, is a concentrated solar power (CSP) facility, that utilizes 10,600 mirrors (heliostats) arranged in a circle to reflect sunlight onto a central tower 243 feet high.
By heating up and melting the chemical salt inside the tower, the temperature of molten salt can reach over five hundred degree Celsius. Water is vaporized, and the steam drives a turbine to generate electricity. The plant is designed to store the generated electricity, which will allow it to provide power 24 hours a day.
However, each of the heliostats need to be connected to, and controlled by, a centrally located server. This entails a huge undertaking in terms of data transmission.
The Challenge
In order to maintain energy production, the solar plant must be able to run non-stop at all times when sunlight is available. The efficiency and profitability of the plant depends on the solar radiation staying focused on the tower. Electrical output will decrease if the temperature of the chemical salts is reduced, so it is important that the heliostats are constantly aligned correctly with the sun and the tower.
The positional adjustment of the heliostats is automated, and monitored by an engineering crew at the control center. Heliostat Control Boxes (HCB) receive sun position information from central servers, and determine the angle of heliostat arrays at any given moment, based on commands sent from the control center. To maximize productivity, and minimize the chance of costly plant downtime occurring, this interconnected system requires a redundant, economical, and robust Ethernet solution that is easy to set up and manage. Due to budget restraints, it is not possible for managed Ethernet switches to be used throughout the entire facility. The solution to be provided required a mix of managed and unmanaged switches, with no sacrifices in performance.
Additionally, the temperature in the Atacama Desert can reach highs of around 104°F (40°C) during the day, whilst falling to temperatures of 41°F (5°C) or below at night. The network infrastructure of a facility running in such harsh conditions must be hardened against sudden swings in temperature.
Application Requirements
- Network redundancy with low failover time
- Reliable connections to heliostat control boxes
- Hardware must be able to withstand extreme temperature swings
Solution
EtherWAN was entrusted with the creation of a highly reliable data communications network, one that could connect all devices in the massive 700 hectare (1730 acre) facility. EtherWAN's field application engineers worked closely with the plant designers in order to understand the application requirements, then designed and tested the proposed network architecture.
The Right Combination of Hardware and Software
Bringing to bear both years of experience and proprietary technology, EtherWAN delivered a high performance solution that fully achieved the main technical objective – dependable data transmission for the over 10,000 HCBs in the solar farm, to the servers and personnel in the control room. Each HCB is connected to an EX43000 industrial unmanaged switch, which is equipped with relay alarms for power and link failure. The EX43000 switches are arranged in an Alpha-chain, a self-healing technology created by EtherWAN designed to provide redundancy in complex networks. Interoperable with other redundancy protocols, Alpha-chain provides fast fault recovery according to a user-defined timeout count.
Each Alpha-chain is linked to a pair of EX61000A industrial managed switches, interconnected with EX27000 all-fiber interface managed switches into an Alpha-ring. Alpha-Ring is a proprietary EtherWAN technology that provides a failover time of less than 15 milliseconds in the event of failure of any component in the ring. Through the Alpha-ring, control room servers are connected with redundant backbone connections.
Full System Protection, Inside and Out
This robust topology is augmented by complete broadcast storm protection. Broadcast storms are caused by an excessive buildup of broadcast network traffic. If left unchecked, a broadcast storm can cause a network to crash. EtherWAN provided broadcast storm protection on both the managed and unmanaged switches employed, ensuring that once the broadcast traffic exceeds a set threshold, broadcast frames will be automatically filtered out. This allows for bandwidth to be conserved for essential transmission.
All three models of EtherWAN switch employed in this solution are hardened against extreme temperatures, and are designed for years of nonstop data transmission at a full range of data loading.
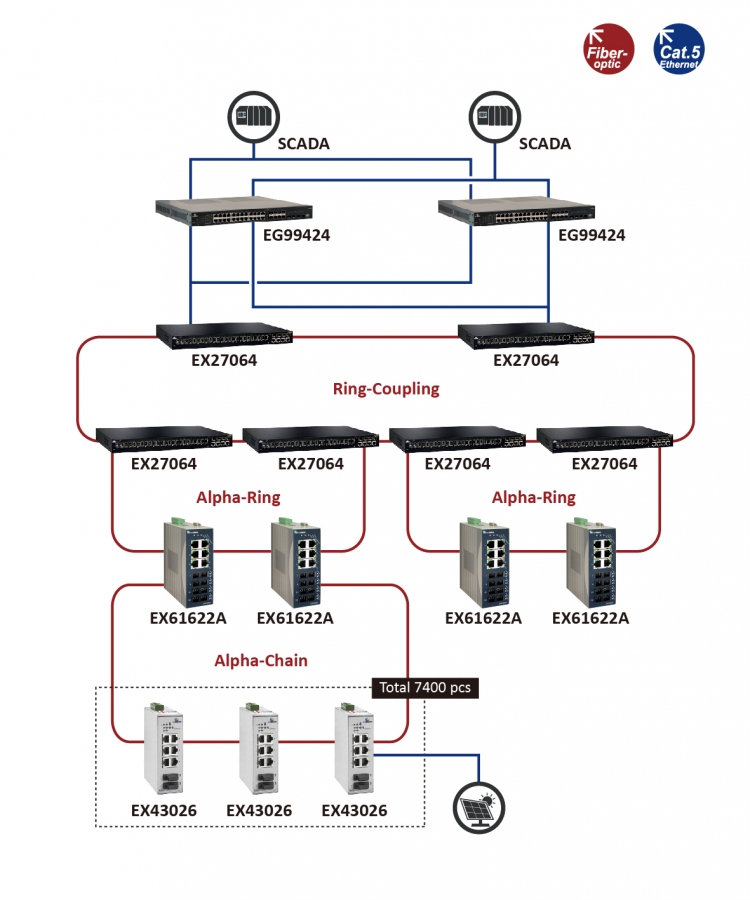
Conclusion
The migration to solar energy brings with it new challenges for network design and implementation. Even with tens of thousands of linked devices, maximum uptime is still essential. Furthermore, no single point of failure can be allowed to cause an interruption in the control mechanisms. To ensure maximum productivity, and to reap the maximum benefit of the transition to solar power, hardened high-quality industrial network components must be implemented in topologies that have chain and ring redundancy, in order to prevent system interruptions. When executed correctly, these factors will help lead the world to a future that is clean and green.
Related products:
EtherWAN – " When Connectivity is Crucial "
► For more information, please contact: info@etherwan.com.tw